A Step-by-Step Guide to Retrofitting Old Buildings for Better Air Quality
- Jennifer Crowley
- Jul 4, 2024
- 4 min read
Updated: Jul 8, 2024
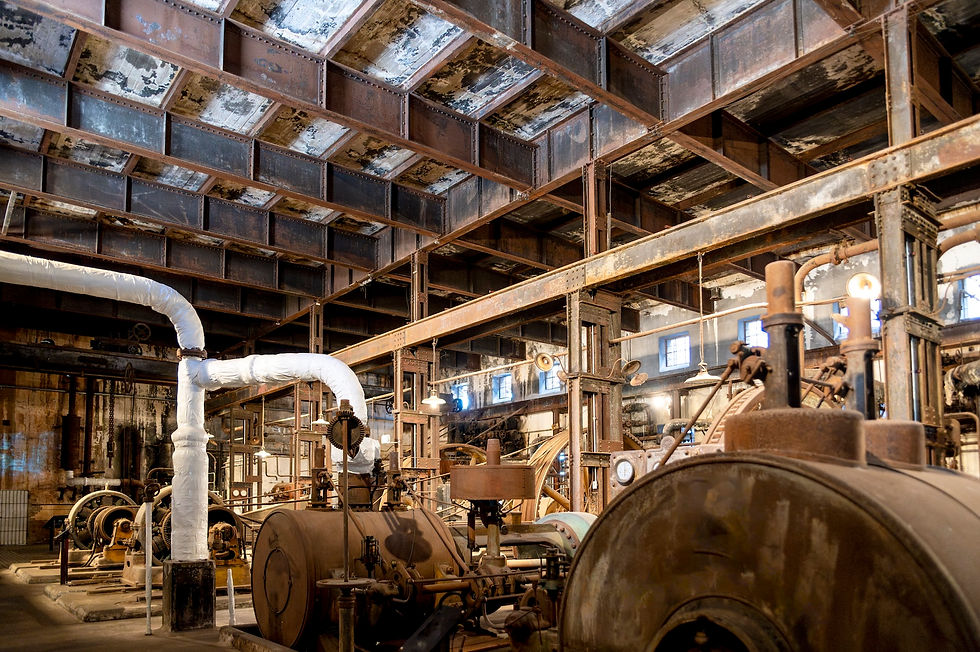
Retrofitting older buildings for better indoor air quality (IAQ) is essential for ensuring the health and well-being of occupants. Over time, buildings accumulate dust, allergens, and other pollutants that can compromise air quality. Additionally, outdated HVAC systems often fail to meet modern standards, leading to inefficient energy use and higher operational costs. Retrofitting these buildings with advanced air quality solutions can dramatically improve IAQ, energy efficiency, and occupant comfort.
Assessment Phase
The first step in retrofitting old buildings for better air quality is to conduct a thorough assessment of the current air quality and HVAC systems. This involves:

1. Air Quality Testing:
Measure levels of common indoor pollutants such as dust, mold spores, VOCs, and carbon dioxide. Use professional-grade sensors and testing kits to get accurate readings.
2. HVAC System Evaluation:
Inspect the existing HVAC system for inefficiencies, outdated components, and potential areas for improvement. Check for signs of wear and tear, and assess the system’s filtration and ventilation capabilities.
3. Building Inspection:
Look for structural issues that could affect air quality, such as leaks, poor insulation, and areas prone to mold growth. This helps identify underlying problems that need to be addressed during the retrofit.
Retrofitting Old Buildings for Better Air Quality - Choosing the Right Solutions
Once the assessment is complete, the next step is to choose the right retrofit solutions. Blade Air offers a range of advanced products designed to improve IAQ and enhance energy efficiency:

These capture ultrafine particles, including viruses and bacteria, far exceeding the capabilities of traditional pleated filters. They ensure cleaner air and better protection against airborne contaminants.
Ideal for capturing up to 99.97% of airborne particles, including dust, pollen, and mold spores. These filters are especially beneficial for occupants with allergies or respiratory conditions.
This technology uses ultraviolet light to kill bacteria and viruses in the air. It is an excellent solution for reducing microbial contaminants and improving overall air hygiene.
Effective for removing odors and volatile organic compounds (VOCs),
enhancing overall air quality and comfort.
These portable units combine HEPA filtration with activated carbon to provide superior air purification in specific areas, making them perfect for targeted air quality improvements.
Implementation:
The implementation phase involves installing and integrating the chosen air quality solutions. Here’s a step-by-step process:
1. Preparation:
Building Readiness: Ensure the building is ready for retrofit activities. This involves scheduling the retrofit to minimize disruption to occupants. Informing occupants of the upcoming changes can help manage expectations.
Minor Repairs: Address any minor structural repairs identified during the assessment phase. This might include sealing leaks, improving insulation, or fixing areas prone to mold growth.
Cleaning: Perform a thorough cleaning of the HVAC system and areas where new equipment will be installed. Removing accumulated dust and debris ensures a smoother installation process.
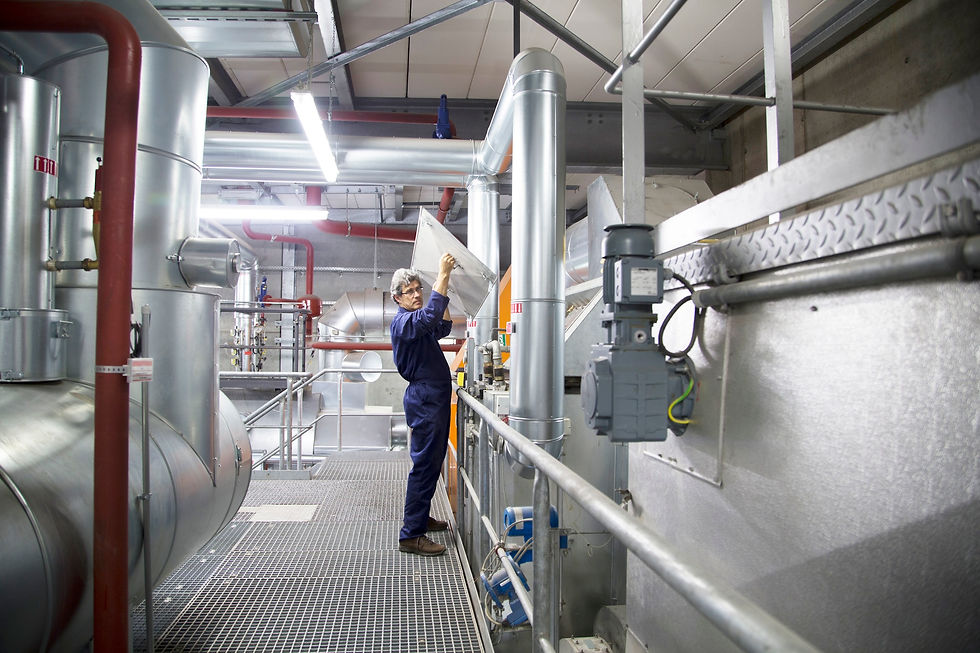
2. Installation:
Professional Installation: Blade Air recommends that our expert team install our filtration products for you. This ensures proper installation and allows us to train your team on installation and maintenance procedures.
HEPA Air Purifiers: Place HEPA air purifiers in strategic locations such as high-traffic areas, common rooms, and near HVAC intakes. Ensure you follow the instruction manual and that they are plugged in and functioning correctly.
3. Integration:
System Connection: Connect the new filters and UV-C light systems to the existing HVAC controls. This may involve updating the HVAC control software or adding new control modules.
Testing and Calibration: After installation, conduct thorough testing to ensure all components are working correctly. Calibrate the UV-C light intensity and HEPA air purifier settings to achieve optimal air quality.
Optimization: Adjust the HVAC system settings to account for the new filters and purification devices. Ensure that airflow and ventilation rates are optimized for the enhanced filtration system.

4. Testing:
Initial Performance Check: Perform an initial performance check of the installed systems. Measure airflow rates, filter pressure drops, and UV-C light output to ensure everything is within specified ranges.
Air Quality Testing: Conduct air quality tests to verify the improvement in IAQ. Measure levels of dust, VOCs, mold spores, and other pollutants before and after installation.
System Monitoring: Set up continuous monitoring to track the performance of the new systems over time. This helps in identifying any immediate adjustments needed to maintain optimal IAQ.
5. Training:
Staff Training: Provide comprehensive training sessions for building maintenance staff. Cover topics such as filter replacement schedules, UV-C light maintenance, and operation of HEPA air purifiers.
User Manuals: Supply detailed user manuals and quick reference guides. Ensure that staff have access to resources that help them manage and troubleshoot the new systems.
Ongoing Support: Offer ongoing support through Blade Air’s customer service. Encourage staff to reach out with any questions or concerns during the initial adjustment period.
Maintenance
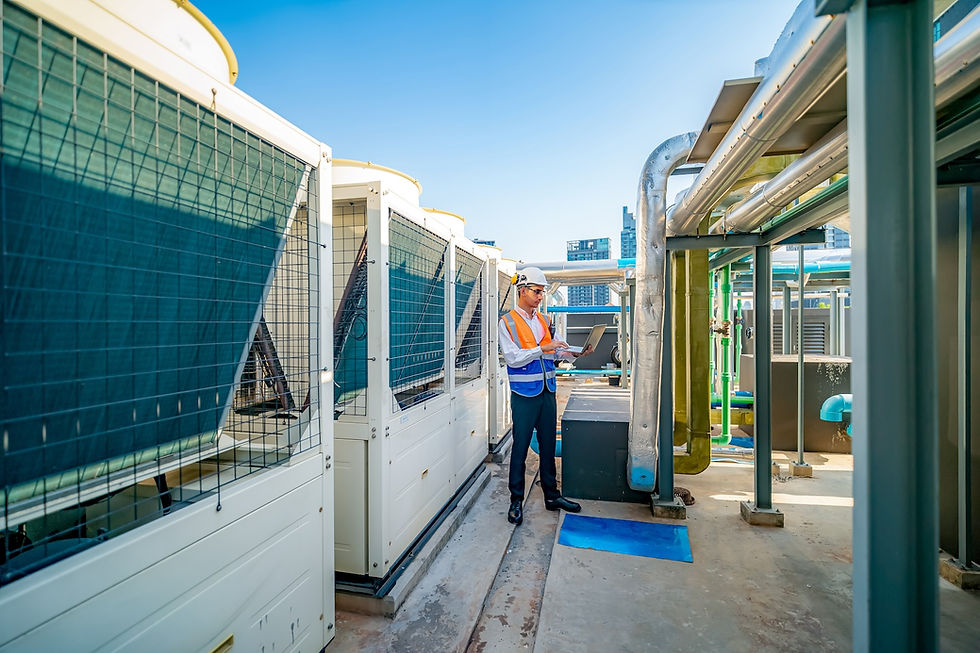
Maintaining the new air quality systems is crucial for long-term efficiency and performance. Here are some tips:
1. Regular Inspections:
Schedule routine inspections to check the condition of filters, UV-C lights, and other components. Look for signs of wear and replace parts as needed.
2. Filter Replacement:
Follow the manufacturer’s guidelines for replacing filters. Regular replacement ensures optimal filtration and prevents clogging.
3. System Calibration:
Periodically calibrate the smart monitoring systems to ensure accurate air quality readings.
4. Cleaning:
Keep the HVAC system and air quality devices clean. Regular cleaning prevents dust buildup and maintains system efficiency.
5. Data Review:
Regularly review air quality data to identify trends and potential issues. Use this data to make informed decisions about maintenance and system adjustments.
Retrofitting older buildings for better indoor air quality is a comprehensive process that involves assessment, choosing the right solutions, implementation, and maintenance. By following these steps, you can significantly improve IAQ, enhance energy efficiency, and create a healthier environment for occupants.
Blade Air is here to assist you throughout the entire retrofit process, offering advanced products and expert guidance to ensure your retrofit project is a success. Contact us today to learn more about how we can help transform your building’s air quality.